Project Overview
- Client: A leading automotive parts manufacturer in Toronto, Ontario, specializing in precision components for electric vehicles (EVs).
- Requirement: Upgrade legacy overhead cranes to enhance production line flexibility, improve safety, and meet stringent European efficiency standards.
- Solution: DQCRANES designed and delivered a 16-ton double girder European-style wire rope hoist with dual lifting speeds (0.45/2.7 m/min) and a lifting height of 6 meters, tailored for high-precision assembly tasks.
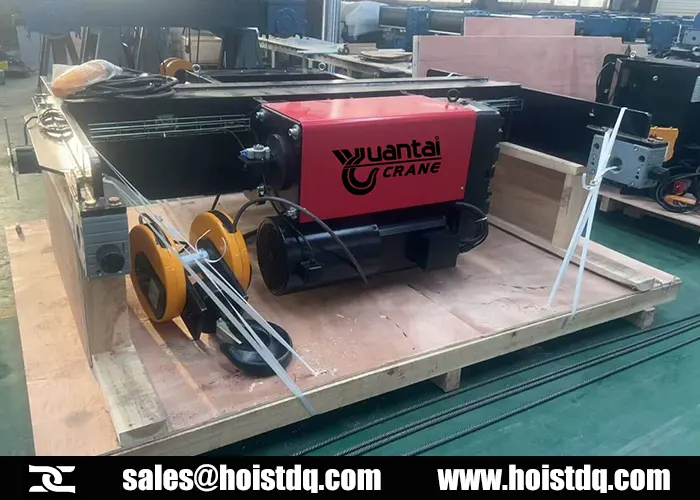
Client Background & Challenges
Industry:
- Automotive manufacturing (EV battery modules and chassis components).
Pain Points:
- Existing electric rope hoists lacked precision control, causing alignment issues during assembly.
- Frequent downtime due to outdated equipment maintenance.
- Space constraints in the factory required a compact, low-headroom design.
Technical Specifications & Customization
DQCRANES proposed a European-standard double girder hoist with the following features:
Parameter | Specification |
Capacity | 16 tons (dual-speed lifting) |
Lifting Height | 6 meters |
Track Gauge | 2m |
Lifting Speed | 0.45 m/min (precision mode), 2.7 m/min (standard mode) |
Traveling Speed | 2.0~20 m/min |
Motor | Three-in-one motor, Frequency converting control |
Insulation grade | F |
Protection class | IP54 |
Safety Features | Overload protection, emergency stop, limit switches, etc |
Structural Design | Double girder configuration with Euro-spec trolley |
Working Class | FEM 2M (equivalent to ISO M5) |
Power Supply | 220V/50Hz/3phase |
Control Method | Remote control |
QDX 16 Ton FEM Hoist Design Solutions
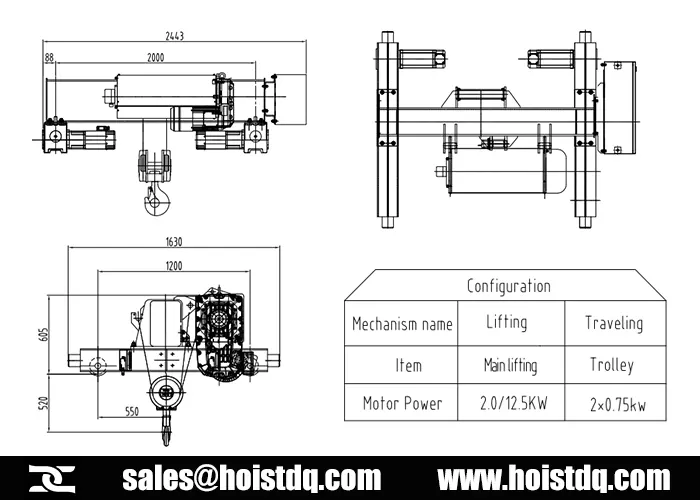
A. Dual-Speed Precision Control
- Challenge: The client required precise positioning (±2mm accuracy) for EV battery module assembly.
Solution:
- Low-speed mode (0.45 m/min): Enabled micro-adjustments during component alignment.
- High-speed mode (2.7 m/min): Accelerated material transfer between workstations.
- Integrated anti-sway technology minimizes load oscillation during movement.
B. Space Optimization
- Challenge: Limited vertical clearance in the facility.
Solution:
- The low-headroom trolley design saved 15% vertical space compared to traditional hoists.
- The double girder structure provided superior stability without increasing the footprint.
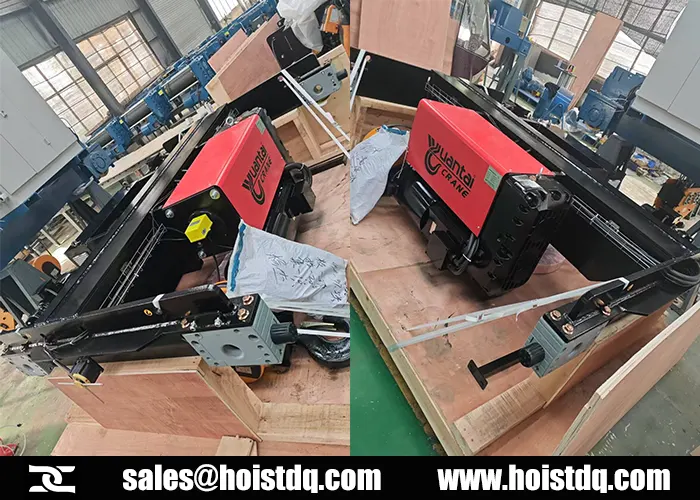
C. Energy Efficiency
- High-class Motor + VFD: Reduced energy consumption by 25% versus hydraulic systems.
- Electromagnetic disc type brake system: Captured kinetic energy during deceleration, making the lifting smooth and stable.
D. Compliance
- Certifications: CE marking (EU) and ISO 9001/45001.
- Local Adaptation: Collaborated with Toronto-based engineers to customize cold-weather components (e.g., frost-resistant wire ropes).
electric hoist Safe Operations
Pre-Operation Safety Checks
A. Equipment Inspection
- Wire Rope: Check for fraying, kinks, or broken strands (replace if damage exceeds 10% of rope diameter).
- Hook: Inspect for cracks, deformation, or wear on the latch.
- Brakes: Test emergency and service brakes for responsiveness.
- Limit Switches: Verify upper/lower travel limits and overload protection systems.
- Electrical Components: Look for exposed wires, loose connections, or corrosion.
B. Load Capacity Compliance
- Never exceed the Working Load Limit (WLL) marked on the hoist.
- For tandem lifts (multiple hoists), ensure load distribution is balanced and certified by an engineer.
C. Environmental Readiness
- Temperature: Use hoists rated for ambient conditions (e.g., -20°C to +40°C for standard models).
- Hazardous Areas: In explosive atmospheres (e.g., chemical plants), use ATEX-certified hoists with anti-spark components.
Safe Operation Procedures
A. Lifting and Moving Loads
- Centering the Load: Ensure the load is centered under the hook to prevent swinging.
- Smooth Acceleration/Deceleration: Use variable frequency drives (VFDs) to avoid sudden jerks.
- Anti-Sway Systems: Activate technology (if equipped) to minimize load oscillation.
B. Speed and Control
Dual-Speed Modes:
- Low Speed (0.1–1 m/min): For precise positioning (e.g., aligning machinery).
- High Speed (5–20 m/min): For general material handling.
- Remote Controls: Maintain a safe distance from the load during operation.
C. Prohibited Actions
- Do NOT lift loads over personnel.
- Avoid side-pulling or dragging loads horizontally.
- Never use the hoist to lift people.
Post-Operation Safety
- Parking: Secure the hoist in a designated area, raise the hook to mid-height, and power off.
- Lockout/Tagout (LOTO): Isolate energy sources during maintenance.
- Post-Use Inspection: Document any issues (e.g., unusual noises, brake slippage).
Types of Wire Ropes Hoists in Canada
How to Purchase an Electric Hoist from DQCRANES
Step 1: Assess Your Requirements
- Application: Define the hoist’s purpose (e.g., automotive assembly, warehouse logistics, mining).
- Load Capacity: Confirm the maximum weight to be lifted.
- Lifting Height: Specify vertical travel distance.
- Duty Cycle: Determine usage frequency.
- Environmental Conditions: Consider temperature, humidity, and hazardous areas (e.g., explosion-proof areas).
Step 2: Contact DQCRANES
- Website/Email: Visit DQCRANES’ official website – www.hoistdq.com or email sales@hoistdq.com.
- Request a Quote (RFQ): Provide technical specifications and site conditions for a tailored proposal.
Step 3: Review Technical Proposal
DQCRANES will typically provide:
- 3D CAD drawings for hoist and runway system, price list.
- Compliance Details: CE/ISO certification and safety features.
- Customization Options: Dual-speed motors, Single phase or three phase hoists.
Step 4: Finalize Logistics and Installation
- Shipping: DQCRANES ships from China factories (lead time 5–10 weeks), or faster delivery is available.
- Installation: Choose between:
- DQCRANES’ remote guide for simple setups or on-site technicians (for complex setups).
- Local contractors (pre-vetted by DQCRANES).
- Testing: On-site load testing and safety inspections post-installation.
Step 5: Payment and Financing
- Payment Terms: 100% T/T before production for lighter tones. Typically 50% upfront, 50% before delivery for heavier tones. (Other types are optional for the client’s needs.)
Step 6: Training and After-Sales Support
- Operator Training: Remote or On-site sessions for safe operation and controls.
- Warranty: Standard 12-month warranty (extendable).
- Service Network: Access to DQCRANES’ service center for spare parts and repairs.
Conclusion
Purchasing an electric hoist from DQCRANES in Canada can secure safety, efficiency, and long-term value. For any questions or a free quote, welcome to contact us at +86-188-3818-4113 directly.